By Tracy Staedter
In March 2020, as the number of COVID-19 cases in the U.S. began to swell, hospitals put out a desperate call for help. They needed personal protective equipment — and they needed it fast. The Northrop Grumman FabLabs community swung into action.
These fabrication laboratories provide innovation space for employees to pursue new ideas and test out potential customer solutions. But they’re also ideal spaces to respond quickly to urgent manufacturing needs, already equipped with a range of industrial tools and equipment, including 3D printers, laser cutters, metal and woodworking machines and even sewing machines. Within two months, six Northrop Grumman FabLabs in California and Florida cranked out more than 10,000 face shields for dozens of hospitals.
It began with a simple request. A nurse working in an intensive care unit asked her friend Daniel Hubert, a Northrop Grumman design engineer in Florida, if he could fabricate a face shield for her. Hubert researched designs approved by the National Institutes of Health and found a simple pattern made from a 3D-printed headband and a sheet of clear transparency paper. He prototyped the first one, and once the hospital approved, the entire 85-person ICU staff requested one. Undaunted, he recruited fellow engineers to assist. In three days, they printed 150 face shields.
It was clear by then that the FabLabs could play a huge role. Tony Long, a project management manager and FabLab lead in California, put out a company-wide call for volunteers. Anne Stockdale, an engineer and manager, stepped in to help coordinate production and distribution. Each day, employees reported on their progress, discussed materials needs and coordinated fixes on any equipment problems.
“It was a quick way to get everybody on the same page and figure out who needed help as quickly as possible,” says Stockdale.
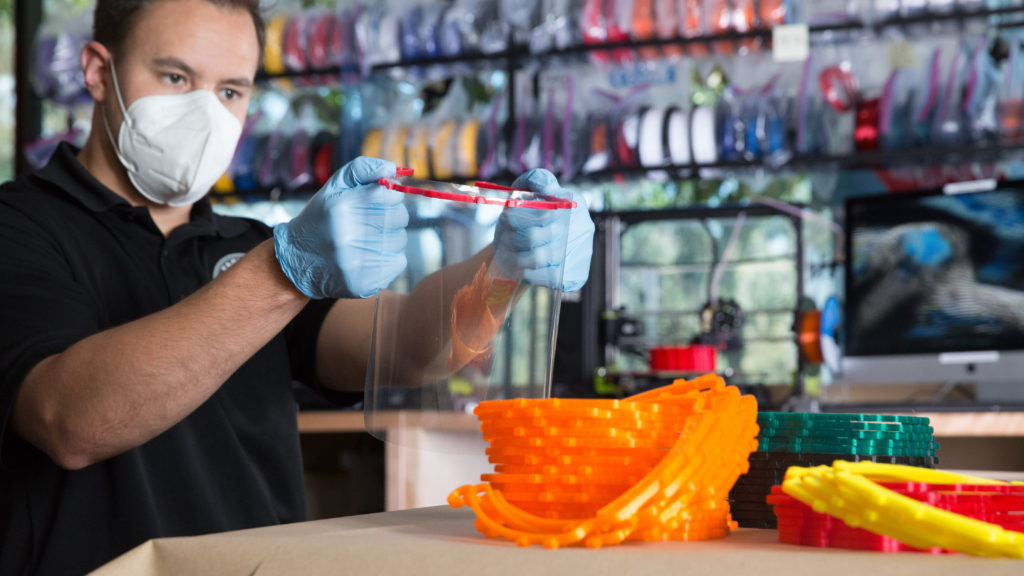
Around the country, dozens of employees pitched in. Charlie Mann, a computer systems analyst in Illinois, who had seven 3D printers in his home, produced dozens of shields in just a few weeks. CJ Nesbitt, an engineering manager in California, also enlisted his own 3D printer as well as six others at the San Diego FabLab. His group made more than 5,500 face shields for local volunteer medical responders and healthcare workers.
In the end, Northrop Grumman FabLabs delivered about 16,700 face shields to healthcare workers in Arizona, California, Florida, New York, New Jersey, Texas and Virginia. They also worked with the Federal Emergency Management Agency to send surplus equipment to hospitals experiencing critical needs. The FabLabs will be ready to rise to the challenge, should a need arise again.
Are you ready to make what’s next? Explore our engineering careers.